Beschreibung des Produkts
Beschreibung des Produkts
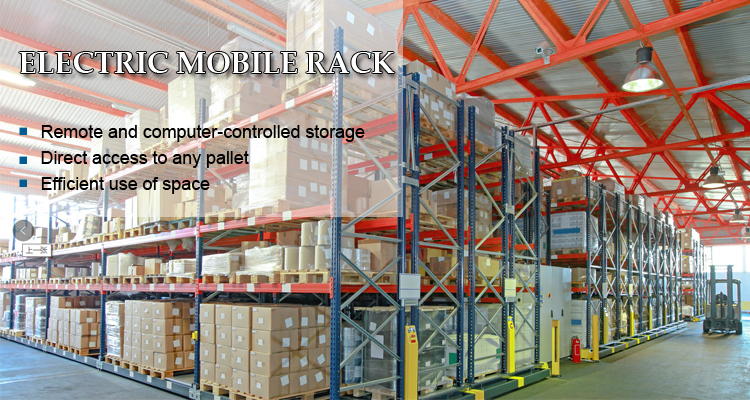

aisles. With Movirack mobile racking and shelving, the aisles open up only when the operator requests access.
The motorized mobile bases are electronically-powered and are guided by rails in the floor.
A full varity of ranges and accessories available
|
|
|
1. Item:
|
Electric Movable Pallet Racking
|
|
2.Style:
|
Quick access,adjustable
|
|
3.Material:
|
Grade Q235 (or SS400) Q345
|
|
4.Certification:
|
ISO9001
|
|
5. Standard Color:
|
Blue, Orange, Green, Grey , Yellow,Red,Customized
|
|
6. Adjustable Pitch:
|
50.8mm,76.2mm
|
|
7. Access Style:
|
High accessibility & selectivity
|
|
8. Finishing:
|
Powder Coated or Galvanized
|
|
9.Application Environment:
|
Normal Temperature or Freezer
|
|
10.Design Service:
|
Free CAD service available
|
|
11.Back-up Service:
|
Installation Drawing/On Site Instruction
|
|
12.MOQ:
|
1 unit
|
|
13.Lead time:
|
3 weeks for 2*40' container
|
|
14.Standard package:
|
Palletized,Export-Purpose Packaging
|
|
15.Container Load:
|
10-15tons/1*20' container, 20-25tons/1*40' container
|
|
16.Trade Term:
|
EXW/FOB/CNF/CIF
|
|
17. Size
|
Customized
|
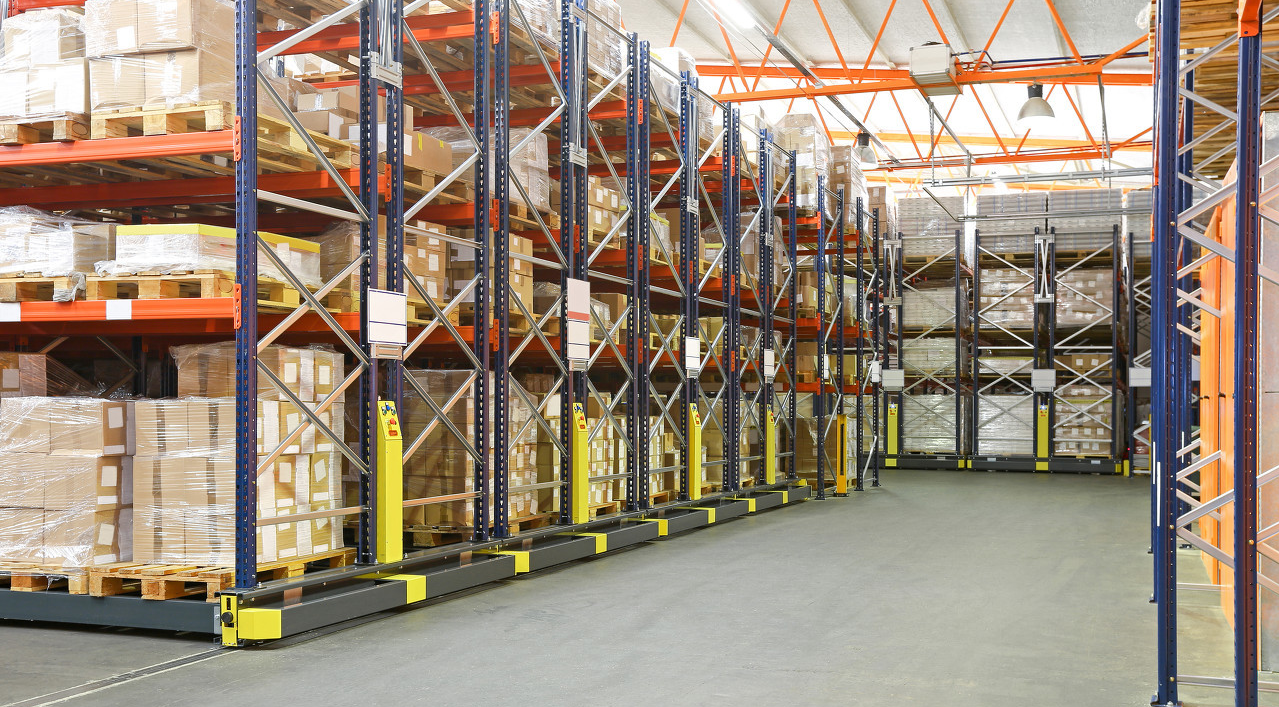
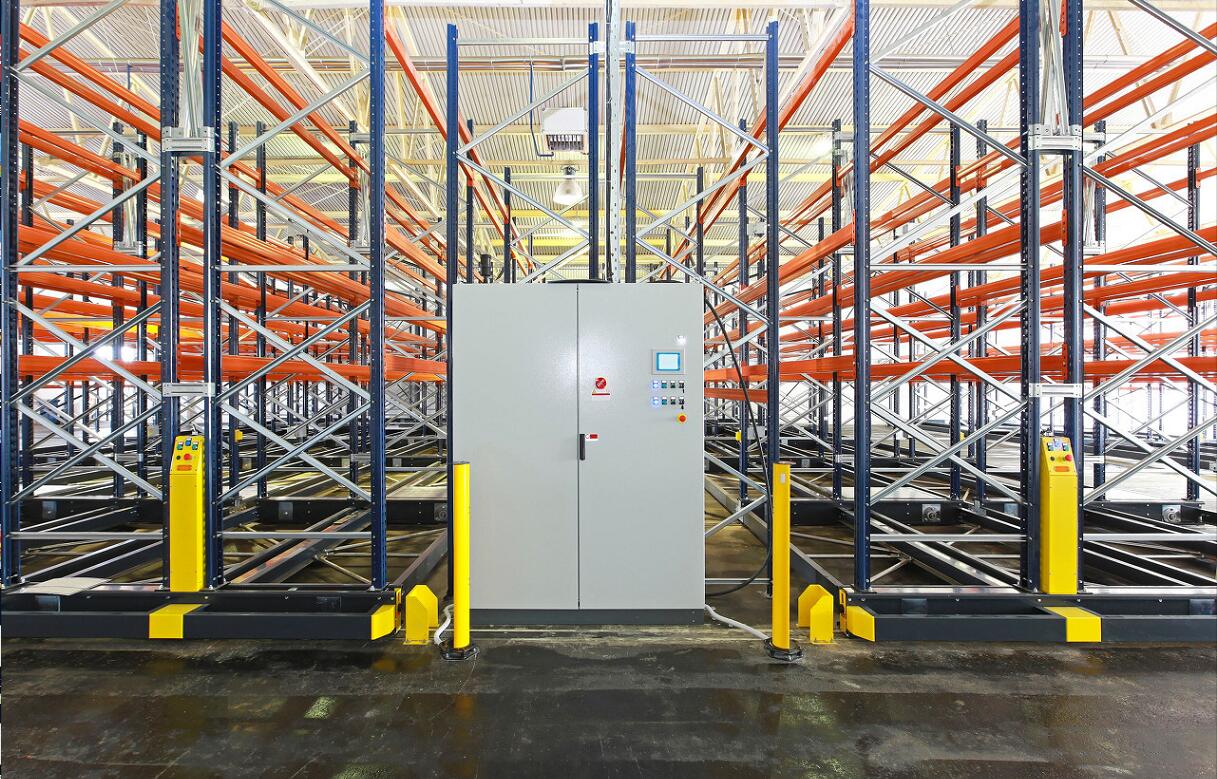
Advantages
* Direct access to any pallet
* Efficient use of space
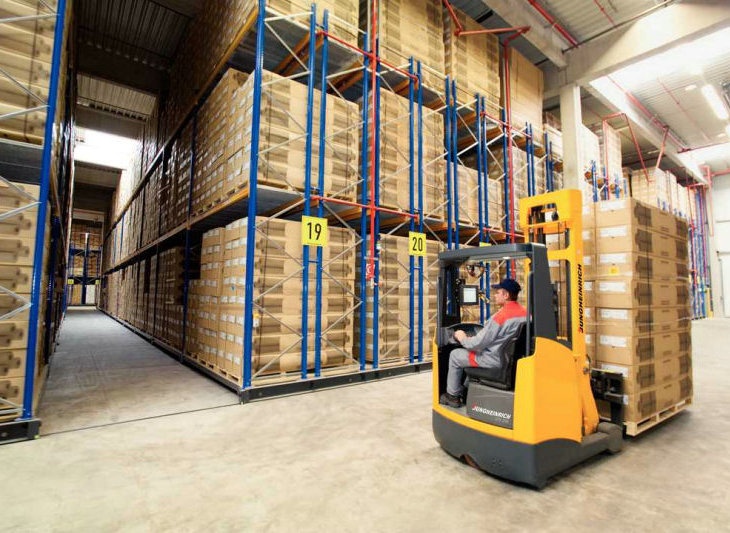
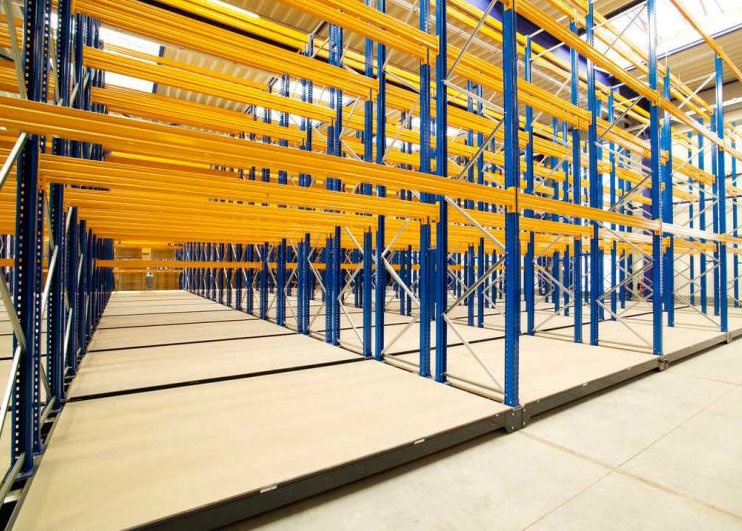
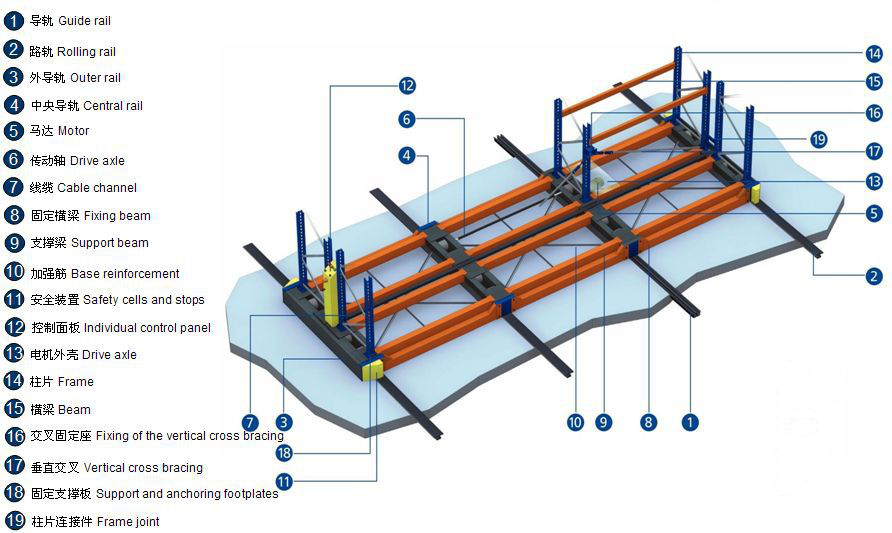
The Movirack units are installed on mobile bases, opening up an aisle provides direct access to the desired pallet.
Utilization of available space is based on to two basic premises: increasing the storage capacity and reducing the storage area required.

In the era of booming e-commerce and just-in-time logistics, warehouse efficiency is a critical driver of profitability. Traditional static racking systems often struggle to balance storage density, accessibility, and flexibility. Enter mobile racking systems—a revolutionary solution that maximizes space utilization while maintaining operational agility. Designed to handle pallets, long goods (e.g., pipes, lumber), and heavy loads, these systems are redefining modern warehousing. Drawing insights from Google’s top-ranked sources and industry data, this blog explores the technology, benefits, costs, and trends shaping the mobile racking industry.
1. What Are Mobile Racking Systems?
Mobile racking systems consist of shelving units mounted on motorized or manual carriages that move laterally along rails embedded in the floor. Unlike static racks, which require fixed aisles, mobile systems eliminate unnecessary pathways by consolidating shelves into compact blocks. A single access aisle shifts dynamically, unlocking up to 80% more storage capacity compared to conventional setups.
Key Components:
- Carriages: Motorized or manual bases that move shelves.
- Guide Rails: Reinforced tracks ensuring smooth, aligned movement.
- Safety Systems: Sensors, emergency stops, and anti-collision mechanisms.
- Load Beams: Adjustable beams for pallets or long goods (e.g., 12-meter steel pipes).
2. Market Overview: Growth and Demand Drivers
The global mobile racking market is projected to grow at a CAGR of 7.8% from 2023 to 2030, reaching $4.2 billion by 2030 (Grand View Research). Key drivers include:
- Space Constraints: Urban warehouses face rent increases of 12% YoY (Colliers International, 2023), pushing firms to optimize vertical and horizontal space.
- E-Commerce Boom: Online retail inventory needs have surged by 35% post-pandemic, demanding high-density storage.
- Automation Integration: 60% of new warehouses now pair mobile racks with AGVs (Automated Guided Vehicles) or AMRs (Autonomous Mobile Robots).
Regional Trends:
- North America: 40% market share, driven by third-party logistics (3PL) providers.
- Europe: Stringent sustainability regulations favor energy-efficient electric mobile systems.
- Asia-Pacific: Fastest-growing region (+11% CAGR), led by manufacturing hubs in China and India.
3. Types of Mobile Racking Systems
A. Pallet Mobile Racking
- Design: Engineered for standard pallet sizes (48"x40" or 1200x1000mm) with load capacities up to 2,500 kg per pallet.
- Applications: Ideal for food and beverage, pharmaceuticals, and automotive parts.
- Case Study: A Canadian 3PL firm increased pallet storage by 76% using electric mobile racks, reducing operational costs by 22%.
B. Long Goods Mobile Racking
- Design: Features cantilevered arms or wide-span beams to support lengthy items (up to 15 meters).
- Applications: Construction materials, metal tubing, and furniture.
- Case Study: A German steel supplier reduced floor space by 60% while improving retrieval speed by 35%.
C. Hybrid Systems
- Flexi-Combi Racking: Combines mobile racks with static shelves for mixed inventory (e.g., small parts + bulk pallets).
4. Technical Specifications and Innovations
A. Load Capacity and Durability
- Dynamic Load Rating: Ranges from 1,000 kg to 3,000 kg per shelf, depending on beam material (steel vs. aluminum).
- Corrosion Resistance: Galvanized or powder-coated finishes for harsh environments (e.g., cold storage).
B. Mobility Mechanisms
- Manual Systems:
- Operated via hand cranks or push-pull mechanisms.
- Cost: 500 per linear meter.
- Best For: SMEs with limited budgets and low-frequency access.
- Electric Systems:
- Motorized movement controlled via touchscreens or IoT-enabled devices.
- Cost: 1,500 per linear meter.
- Best For: High-throughput warehouses (e.g., Amazon fulfillment centers).
C. Safety and Compliance
- Anti-Collision Sensors: Laser or infrared sensors halt movement if obstructions are detected.
- Seismic Compliance: Systems in earthquake-prone zones (e.g., Japan) require reinforced bases and dampers.
5. Cost Analysis: ROI and Total Cost of Ownership (TCO)
While mobile racking systems have higher upfront costs than static racks, their long-term ROI is compelling:
Cost Factor | Manual System | Electric System |
---|---|---|
Initial Investment (per m²) | 600 | 1,200 |
Energy Consumption (annual) | $0 | 2,500 |
Maintenance (annual) | 100 | 500 |
Space Savings | 50–70% | 70–85% |
Payback Period | 3–5 years | 2–4 years |
Case Study:
A U.S. automotive parts warehouse invested 180,000 annually in reduced rental costs. The system paid for itself in 2.5 years.
6. Leading Manufacturers and Product Comparisons
Manufacturer | Key Product | Load Capacity | Price (per m²) | Unique Feature |
---|---|---|---|---|
AR Racking | Electromobile Pro | 2,500 kg/pallet | $1,100 | IoT integration with warehouse management systems (WMS). |
Montel | SmartShelf Mobile | 3,000 kg/pallet | $1,300 | Modular design for easy reconfiguration. |
Hänel | Rotomat Mobile | 1,500 kg/pallet | $950 | Compact footprint (ideal for small spaces). |
SSI SCHAEFER | Mobile Pallet Racking | 2,800 kg/pallet | $1,400 | Energy-efficient regenerative braking. |
7. Challenges and Limitations
- High Initial Cost: SMEs may struggle with upfront investments exceeding $100,000.
- Maintenance Complexity: Electric systems require specialized technicians for repairs.
- Floor Requirements: Rails need reinforced concrete floors (≥30 MPa strength), adding installation costs.
8. Future Trends: Automation and Sustainability
- AI-Driven Systems: Predictive analytics optimize shelf movements based on inventory turnover rates.
- Green Warehousing: Solar-powered mobile racks and recyclable materials reduce carbon footprints.
- 3D Mobile Racking: Multi-directional systems enabling vertical and horizontal movement (patented by Kardex Remstar).
9. Conclusion
Mobile racking systems are no longer a luxury but a necessity for warehouses battling space constraints and rising operational costs. With the ability to store up to 85% more goods and integrate seamlessly with automation, these systems offer a future-proof solution for industries ranging from retail to heavy manufacturing. While the initial investment is significant, the ROI—measured in space savings, labor efficiency, and scalability—makes mobile racking a cornerstone of modern logistics.